
Exhausts
Exhaust Sensors:
Maintenance:
Exhaust Gases or Manifold Leak
Exhaust and Converter Replacement: Brands
Exhaust and Converter Replacement: Procedures
Exhaust Manifold, Studs, Brackets, Front Pipe:
Exhaust Manifold Gasket & Studs Replacement
Leaks in Manifold to Downpipe Joint
Exhaust Brackets Keep Breaking
Exhaust Manifold Cracks and Repairs
Converter/Engine Pipe Joint Repair
Exhaust Sensors:
Oxygen Sensor Replacement. See the specific sections on diagnostics in the FAQ Fuel Injection and on replacement in the Sensors files.
EGR Valve. See EGR Valve in Electrical: Sensors, Etc.
Maintenance:
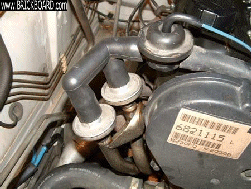
[Inquiry] I noticed a noisy hose in front of the engine of my 1995 940 B230F. The noise goes away when downward pressure is exerted, and air can be felt at the corner junction. What is this thing?
[Response] This is the air injection valve, with a one-way check valve (the wider discs) for air injection into the exhaust to heat the catalytic convertor and O2 sensor on cold start and provide sufficient O2 to the catalytic converter so it can do its job. It is used on selected non-turbo engines for pollution control and is controlled by a solenoid. While the connection is still loose, idle the engine and take the time to pull the rubber hose off, and be sure hot exhaust isn't blowing back through the discs...if it is then replacement is in order, else hot gasses will soon burn through other parts. A good cleaning and a bit of black RTV should repair your hose 'for the life of the product'. Usehose clamps on reinstallation.
Exhaust Gases or Manifold Leak.
Exhaust Vapors in Car:
[Inquiry] Getting fumes in the car while idling, not while moving.
[Response: Brian Oliver]I've seen two types of reasons for this:
- Leaking exhaust joint: It could be manifold to head, manifold to pipe, or pipe to cat. I've had all those on various cars, and some others too on FWD cars with flex pipe sections. See also the Turbo section for lots of data.
- Crack in the front pipe: On our 940, it was in the crotch of the Y-joint, and couldn't be seen until the pipe was out and the heat shield ripped off.
Diagnosing Leaks. If you ever get cold weather, look carefully for little puffs of vapour in suspect locations just after you start the car up on a cold morning. That's how I found the last two. [Marty Wolfson] Using the vacuum outlet of my shop vacuum, I duct tape the hose to the cold exhaust pipe and turn it on. Use a lighted incense stick to pinpoint areas where there might be small exhaust leaks: the vacuum sucks the smoke right into the exhaust leak. You can also feel around with a cold but just started engine (before it gets hot) around the various joints for potential leaks
[Problem:]I own a 1990 740 wagon with the B230F with an exhaust leak at the manifold. Is this a common problem? Do the exhaust manifolds warp easily?
[Diagnosis:] The exhaust manifold gaskets on the B230F tend to blow out every once in a while. Mine has a leak next to #1 but since it's not major or real noisy I'm waiting for the rest of it to go or get worse. If you have to change the gasket be prepared to get new bolts/studs and keep a stud extractor handy as they always break off.
What Do Leaking Exhaust Gaskets Sound Like? [Chris Wilson] Mine was more of a tut...tut..tut...tut noise but came on during acceleration. [Another] Yeah, tut tut tut ....tick tick tick sorta thing. Really can hear it at around 1500RPm and slightly above starting from a stop.
Detecting Manifold Gasket Leaks. [Tip from Mike McBane] To locate an exhaust manifold or gasket leak, duct tape a shop vac hose onto the exhaust pipe outlet, set it on blower, apply soapy water to the manifold gasket and turn it on. Bubbles or air leaks will show the location of the cracks or failing gasket. [Randy Starkie] Using a rubber hose with one end in your ear, try to locate the leak by sound: move the end of the hose around all the manifold connections at the head. Check for loose exhaust manifold nuts.
Exhaust-Like Smell: Leaking Injector Seals.
[Inquiry:] I have a problem with my 760 Turbo that my mechanic can't solve: when accelerating hard, with the ac and the fan on, a strong smell of exhaust comes out of the vents. when the fan and the ac are off, there is no smell. Can anybody help with this? The mechanic says that it can not explain why there should be any smell of exhaust coming in, which, by the way, happens also with the recirculation button turned on.
[Response: Steve Seekins] I suspect that what you smell is not exhaust, but raw gas. I had this problem on a couple of turbo cars. The source was injector seals. When they get bad on a turbo, they suck air into the manifold at idle and off throttle (whenever the turbo gage is in the vacuum zone). However, under boost, the manifold is pressurized and fuel mist from the injectors is forced out past the injector seals and then gets sucked into the vent system by the intake at the front of the windshield. It is worst under heavy load when manifold pressure is highest and more fuel is being injected, and you only get it when the vent system is operating or the windows are open.
Check at idle with can of spray carb cleaner or unlit propane torch jet. Spray or direct jet at each injector base in turn. Any change in engine rpm indicates leaking seal. Also check intake manifold gasket area and look for combination of bad hose from fuel pressure regulator and leaking pressure regulator.
Using Furnace Cement on Joint Leaks. [John Martin] I have used a product made by the Rutland Fire Clay Company and sold in the
stove/fireplace section of the hardware store, costs about $10.
Tube says "Rutland Black, Hi-Temp Stove & Gasket Cement, adheres all types of gaskets to steel and cast iron, withstands 2000F (1095C)." It is Rutland item #77.
Use it on the system when cold, clean the area well, and apply this stuff to WET metal. I've used it on a pesky manifold-to-downpipe joint with success, it seems to withstand pressure, vibration, and intense heat quite well.
Exhaust and Converter Replacement: Brands
Exhaust Replacement Brands. [Editor: Numerous questions about which brands to buy are addressed below.]
[Response 1:] I replaced the exhaust system on my '87 740 Turbo last summer with a Volvo OEM kit. The kit which includes all the hangers and clamps for the car was about $285 and only took me about an hour to install. The kit includes everything from behind the cat. [Response 2:] I bought the Volvo OEM kit because I have heard that they last longer than the muffler shop or aftermarket kits. Having had a few 240s over the years, I have visited the muffler shops a lot. However, the 240s have so much exhaust plumbing compared to a 740, I would expect the 240 to go through them faster. I figured that at $285, it would cost me about that much to have a muffler shop do the work. Then I will have to deal with the periodic returns to have the system replace under warrantee. Figured it was worth a try. [Response 3:] I bought a replacement system mfg. by Starla, just received yesterday. All parts made in Sweden. EVERYTHING from the rear of the cat back, including clamps and hangers, was $245 including shipping. Bought from RPR. [Response: Vladimir Kordac] Stay with Volvo or a quality after-market system. Forget Maremont etc. with their 2yr lifetime crap unless you want to eek out a few more years out of the present system! I put in a complete Bosal system recently from down pipe to tail pipe including cat, that went in flawlessly. Total cost was approx. $325. Bosal is supposedly comparable to OEM. We'll see. [Response: Rob Bareiss] Either the IPD system or the factory Volvo exhaust kit will make you happy. You will also find parts stores which stock Starla brand original fit exhaust components. The stuff is great quality. Goes on just like Volvo's. Lasts as long as your originals did, and costs about the same (a bit less). We use a lot of Starla and Volvo brand parts at our shop, and the difference between those, and the M or W brand junk we throw away is amazing. Get the real stuff, you'll be much happier you spent your money WELL and ONLY ONCE.
[Editor] Consensus seems to be that Volvo OEM is number one in quality, followed by Bosal, then Starla/Walker, then everybody else. Some limited (non-statistically-significant) anecdotal reports about Starla show lighter metal, poor welds or misaligned pipes or hangers. Buy your Volvo OEM kit from one of the low-price dealers or Volvo shops (see the Parts FAQ file for referrals). The Volvo OEM system has a lifetime warranty on mufflers, not on pipes.
Catalytic Converter Replacement Brands. [John Sargent] Original Volvo catalytic convertors are superior to any aftermarket replacement cat. Replacements usually fail emissions testing in a few years. We have four turbo 700s all passing emissions testing and running the original Volvo cat. [Jerry Andersch] I bought a Davico aftermarket catalytic converter from FCPGroton. When I installed it I noticed the construction was not very good: bad welds and a restricted inlet. Five year/50k mile warranty on shell only. The matrix broke up and totally clogged the exhaust system in about six months. I would not buy a Davico product again. Bosal may be a better choice. [Editor] Ditto: Davico converter rotted at the rear pipe-to-shell weld in four years. [Brian King] I purchased a new direct fit Carsound cat from AutohausAZ.com for about $100. The Carsound website had some pretty good info and a search of the forums didn't turn up any negative reviews, so I thought I give their product a try. Other brands are DEC (Diversified Environmental Catalysts) and Walker.
Exhaust System Kits.
[Response: Gary DeFrancesco] The kit Volvo sells has everything you need behind the cat. It even includes the hangers. My dealer hit me just less than $300 for the kit, and it went in like a dream. It took me less than an hour to do the job. [Another Comment:] Installing the Volvo kit was a dream. All the parts FIT! None of the pipe ends were dented requiring hammering to make them go together. The pipes had smooth curves, not ribbed curves as often found on after market kits. Furthermore, the system is probably better sized for the car which hopefully will result in less trouble for us turbo owners. [Comment: Wray] Fit of the Volvo exhaust kit was superb--nothing banged, rattled, leaked, or buzzed. Only mistake I made was not realizing that the cat pipe clamp is 58 mm, all the rest are a few mm larger. That cost me about 15 minutes to figure out and reinstall some clamps. [Editor] The Volvo OEM kit from Borton Volvo cost me a total of $200, has a lifetime warranty on all parts, lasts about eight years in the salt belt, and fits like a dream. That sounds like a no-brainer. The only debate you may have is over the converter, which is much more costly from Volvo.
Exhaust Manifold Gaskets and Studs. [Editor]. Volvo sells the highest quality gaskets (p/n 271704): highly recommended you buy a set from Tasca or Borton or your local dealer. Other brands do not last as long, especially in turbo applications. Watch out if you buy aftermarket studs: many are too short for the application and are not plated for corrosion resistance. See the photo for a comparison of OEM (longer) vs. Aftermarket. See also the cupped washers: necessary to accommodate expansion/contraction of the manifold. Buy replacements from Volvo (p/n 41941)
Exhaust and Converter Replacement: Procedures.
Warning on Electrical Welding. [Editor] Before doing any electrical welding on the exhaust system, disconnect the engine FI and ignition computers and SRS crash sensor so stray currents do not cause these expensive components to fail. Many shops ignore this advice and may cause unexplained performance problems after simple exhaust work.
Tools:
[Jay Simkin/Jeff Pierce] Among the tools you'll need are: (a) a reciprocating saw with a metal blade (in effect a power hacksaw) or an angle grinder with an abrasive wheel, to remove the old system (b) if available, a Dremel is very helpful because it works like a very small angle grinder, allowing you to perform the fine surgery when you have to cut through the outside pipe, without cutting through the inside pipe, to remove slip fit connections like the ones used on Volvos; (c) socket tools (d) PB Blaster or top quality penetrating oil to help you remove the nuts that connect the catalytic converter to the rest of the system, and that connect the engine pipe to the manifold.
Jacking:
[Tip: WRay] Most folks say to use ramps at the front and stands under the jack points at the rear, but I couldn't find a high quality set locally, so I just jacked up the rear from the differential and used jackstands under the factory jack points. There was plenty of working room because the exhaust on the 740 is so close to the right side of the car, and the cat pipe comes back quite far.
Rust and Seized Parts:
[Tip from Brake and Front End Magazine, August 2001] Remove the affected parts using your favorite method. Rusted nuts can often be easily removed by heating them to a glowing red state with a torch before attempting the use of a wrench. Severely rusted nuts and bolts can often be removed by using the wrong wrench or socket. A half-inch socket could fit too sloppily on a half-inch nut, but a 12 millimeter socket might be just what that half-inch nut needs. If you have a rusted nut that you need to remove from a good stud, in a catalytic converter for example, that is simply too rusted to come off by any means of turning it, judicious use of the cutting torch can come to the rescue. You can, with some practice, cut a nut off a stud without damaging the threads on the stud. It takes a steady hand and practice, but it can be done, and quickly. On the easier ones, penetrating oil can still help. It should be noted that there is a big difference in the effectiveness of different penetrating oils. [Editor:] The universal Brickboard consensus is that THE penetrating oils to use are PBlaster or Kroil.
Pipe Removal:
[WRay] I bought an exhaust pipe cutter ($20, basically a chain with a bunch of tubing cutter wheels on the links and a screw mechanism to tighten around the pipe). Pipe cutter was so much fun, I ended up cutting the old exhaust into very short sections for very easy removal. Used my Dremel tool with reinforced cutoff wheels to buzz through any old mounting clamps or hangers. You can also find these for rental at Advanced Auto Parts, Autozone, and O'Reilly's Auto chains. [Editor] A reciprocating saw with a metal cutting blade makes quick work of pipes and hangers. But use safety glasses and ear plugs.
[Tip from Brake and Front End Magazine, August 2001] If you need to remove a slip fit joint (one pipe inside another, held with a clamp) without damaging it, it can be done. You'll see a ridge in the outer pipe caused by the clamp. Heating all the way around the pipe in the area of the ridge (until glowing red) should expand and soften the pipe enough that the inner pipe can be removed by twisting and pulling with a chain wrench or large slip joint pliers. If you can afford to damage either the inner or the outer pipe, you can save some time by slitting the unneeded one along the length of the joint with a cutting torch or cut-off tool. Only the torch will work on the inner pipe.
Converter Joint Removal:
[Gary DeFrancesco] To remove the front muffler pipe from the cat. pipe, I put a reinforced cut off wheel on my Dremel tool and slit the muffler pipe just deep enough so as not to cut the cat. pipe. Pried open the slit on the muffler pipe and everything came apart. (Also need to slit the joint behind the front muffler so that it can be separated from the over-the-axle pipe, but here you don't have to be so careful with how deep you cut.)
[Another comment] In your case, you have to deal with the muffler pipe being welded to the cat. One approach would be to cut the muffler pipe off several inches down stream from the weld. Then using a die grinder, remove the remains of the muffler pipe from the cat pipe. A Dremel tool will also work, but it will take longer. The first thing to do is slit the muffler pipe open length wise. Then carefully slit the muffler pipe next to the weld to free it from the cat pipe. The idea is to not cut into the cat pipe while doing this. It will take a gentle touch and some time. Once the muffler pipe is off, then the weld can be removed with a grinder wheel. However, if the weld is far enough onto the cat pipe, you may have little or no need to remove the weld bead if the new muffler pipe does not go on the cat pipe as far. This will be a PITA job. But the cost of a new Volvo cat may convince you to get creative. (Don't know what a cat for you car cost, but Volvo wanted over $850 for my '88 740T!)
This leads to another approach to the job. Replace the cat with a good quality after market unit. There are some decent ones out there for reasonable cost. Just make sure it is a direct fit unit and the pipe diameters are not restrictive entering or exiting the cat chamber. With a new cat and the Volvo exhaust kit, you should be able to replace the exhaust system in an hour or two.
[Response: Vladimir Kordac] You'll have a small problem with that welded cat. May have to cut back beyond the weld and use a small adapter piece to mate cat and front muffler (resonator). What kind of shape is the rest of the exhaust? Unlike hunting an electrical problem that may take me hours-years, changing an exhaust is a no-brainer. And results are dramatic. Usually the worst part is getting the old stuff off; however, since I was replacing everything, I didn't have to mess with cat connections or any other frozen areas. In the past I would get out the Dremel or rotary cutoff tool to slice through clamps and pipe ends. It would help a great deal to elevate car on all fours.
[Editor] You may find that your cat is mounted to the header pipe using two triangular flanges bolted together. These are always rusted solid. To remove them, cut the bolts off using a Dremel and reinforced cutting wheel right between the two flanges. Then cut the front flange off. To reinstall, buy a split flange that fits the diameter of the header pipe: NAPA can get these as can Volvo dealers. The replacement cat will come with its half of the flange assembled pre-installed on the pipe.
Header Pipe Replacement.
[Editor] When replacing the header pipe, remember that you will need three new bolts and nuts to connect it to the converter behind it. If you need to replace the header, you might consider a new converter to make installation easier: aftermarket units are quite inexpensive. Buy the Volvo OEM manifold-to-header gasket: it is a copper composition and far superior in quality to aftermarket gaskets. You will also need three new copper nuts (Volvo p/n
977211)
to bolt the header to the manifold; torque to 22 ft-lbs. The three small bolts (p/n 945444) holding the middle of the header pipe to the u-shaped wire brace (p/n 1276583) are 8mmx1.25mm pitch by 30mm. The flat washers (3) on the wire brace are Volvo p/n 1306768. Make sure you use nickel high-temp antiseize on all bolt and clamp threads.
Pipe Diameter Incompatibilities:
[Editor] Mixing OEM and aftermarket components can result in diameter incompatibilities. One solution is to take the component with the larger but insufficient inner diameter to a muffler shop and pay to have them stretch the diameter on their equipment. For home mechanics, the Harbor Freight "exhaust pipe stretchers" work only on the thinnest walled tubing; the far more expensive and robust Lisle version can be used with an impact wrench to better effect. The former can be rented from Autozone and Advance Auto. Yet another solution is to buy an inexpensive pipe adapter, sold at auto stores in the exhaust section, that matches ID and OD. Brands are Rol, Walker, etc. and they come in a variety of sizes. You'll need two clamps per adapter.
Installation:
[Response: Warren Bain] On installation, don't forget the anti-seize compound on the threads, it makes removal a dream. I use it on all my exhaust systems and the bolts just turn right off without any problems. [Editor] BEFORE you tighten everything up real tight, make sure your exhaust system has adequate clearance and will not touch heat shields, frame members, etc. Pay attention to the location of the tip of the oxygen sensor (which can touch the heat shield) and the bent joint behind the cat which goes down below the frame member and into the front muffler. Now is the time to move pipes back and forth or rotate them to ensure clearance. Rubber Hanger Installation. [Luiz Sudbrack] The most frustrating aspect (other than the requisite metal bending and
cursing) was getting the rubber hangers in. My solution after a little
soul searching was to place the hangers in a bowl, pour boiling water
(from an electric kettle) over them, allow them to sit for 10 minutes,
and the put a dab of dish soap into the holes that slide over the metal
hangers. It made a huge difference.
Converter is Missing an Oxygen Sensor Plug:
If your replacement aftermarket cat has a threaded bung hole for a second oxygen sensor but your car has only one sensor, obtain a plug from a local Midas Muffler or buy a compatible oil drain plug to fill the hole. The threads are 18mm by 1.5mm. Auto stores have oil drain plugs in this size. Use Loctite Red to secure the threads.
Catalytic Converter Diagnosis. [Tip from Fluke Corporation:] Using a Fluke Digital Multimeter with the 80T-IR/E Extended Range Temperature Probe, you can easily and quickly assess catalytic converter efficiency. For this test, first run the engine until the engine is warm and stabilized. (For engines with electric cooling fans, let them cycle a few times prior to the test) Then shut off the engine and disconnect a spark plug wire on one bank of cylinders. (Note for V engines: If there are dual converters, you will need to perform this procedure on each bank of cylinders.
Restart the engine and block the throttle to maintain 1000 RPM with the one cylinder not firing. Measure the inlet temperature of the converter and compare it to the outlet temperature. You should see a differential of 50 degrees F. or more if the converter is working properly. If the temperatures are less than 50 degrees apart, then the converter needs to be replaced. Before replacing a converter, be sure to determine why it may have failed. If it is a very high mileage vehicle, it is probably just expired. If it is low mileage, you should perform a thorough check of the vehicle to determine the cause. For normal engines with a misfiring cylinder at 1000 RPM, you can expect that the temperatures observed will be in the 600 to 900 degrees F. range.
Simple Diagnosis for Plugged Converter. Look for a screw-in pipe plug in the exhaust pipe ahead of the converter. If, when you remove that, the engine's performance improves, it shows there is a restriction in the converter.
Heat Shields. [Tip from Bruce Young] If your heat shields (the metal plates between the exhaust and the body floor panels) are loose or missing, you can replace them with universal aftermarket versions made by Walker (check with NAPA Auto Parts stores).
Exhaust Manifold Studs, Brackets, Front Pipe:
Exhaust Manifold Nuts, Studs, and Gasket Replacement . [See the sections below and Turbo: Broken Turbo Exhaust Stud]
Parts. Buy ONLY Volvo OEM parts for these applications. They are specially treated to resist heat and corrosion. For all B230 engines, the exhaust manifold nuts are Volvo p/n 948645; washers are p/n 949362. For non-turbos, studs are p/n 953049. For the turbo engines, the studs are p/n 953048. If you need the nuts for the turbo-to-manifold stud, the p/n is 977209.
Removing the Existing Nuts and Studs:
Applying Penetrants. [Response 1: Onkel Udo] Spray the studs using penetrating oil repeatedly (PBlaster highly recommended) for the preceding days. When removing the nuts, use a quality six-point socket. One trick for breaking them free is to first tighten them a very slight amount just to get them to "crack", then apply more penetrant and rotate counterclockwise to remove. When you reassemble, use nickel-based high-temperature antiseize compound on the new studs. [Jay Simkin] To ease nut removal, after several drenchings with PB Blaster I wire-brushed the end of each stud that protrudes past the nut. I used a Dremel and a stainless steel brush. Once the nuts "cracked free", wire-brushing the stud ends eased nut removal: the nuts did not have to push aside 20 years of corrosion on the exposed stud ends. Easing nut removal cut the risk of shearing a stud. [Phil Connell] I've started using beeswax to loosen rusty nuts/threads. Heat up the stud with a torch, then press a chunk of beeswax on the end of the stud. Capillary action draws the melted wax into the thread ands makes removal a breeze. I get the chunks of beeswax off ebay for very low prices.
Using a Chisel. [Rob Bareiss] If any of the exhaust nuts do not readily break free using your ordinary socket wrench, STOP RIGHT THERE. Do NOT apply a lot of force. Instead, get a hammer (small 2-lb sledge is just right) and a fine chisel. You do not need to split all the way through a nut to loosen it. Just a little work straight into the middle of a flat on the nut is usually all that's needed. Ideally a couple of whacks with the chisel, then the nut spins off by hand. AVOID hitting the stud's threads at all costs.
Using Heat. [Response 2: Don Foster] If the original studs appear eroded (rusted away) and you think you can remove them without snapping even one, then new studs would be a cheap investment. I dearly love my oxy-acetylene torch for removing rusted nuts and bolts. Every time I use it, I kiss it. [Another tip] Heat the nut with a Mapp Gas torch and apply beeswax or paraffin wax, which wicks up between threads and eases removal when cold. Use Vice Grip plyers on broken studs. The stud is regular right hand thread, by the way: counterclockwise removes it.
In the Event of a Broken Exhaust Manifold Stud:
A. If the stud has some remnant above the surface: start with low-impact techniques, listed below. Do NOT use an "Eezi-Out" or hardened tool that may break off inside the stud remnants.
Removal by Tapping and Two-Nuts. [Paul Seminara] Soak with PB Blaster, smack area near thread with hammer, PB Blaster, soak, wipe, heat, PB Blaster, hammer tap. If threads are available, then extract with two nut method (install two nuts tightly, then unscrew the lower nut which jams against the upper). But first tighten a bit, apply more PB Blaster...etc, ...repeat..patience is really the key! If no threads are available you can use locking pliers clamped tightly against the stud.
Removing Broken Studs by Slotting. [George Downs] If the stud is not too tight in the hole you could (with adequate grit protection) use a Dremel Moto-Tool with an abrasive disk (#409), cut a slot in the end of the stud, and remove it with a screwdriver.
Removing Broken Studs and Bolts by Tapping with a Punch. [Tip from Don Foster] Try hitting the stud off-center with a tiny sharp punch and little hammer in a small notch in the stud. Tap lightly and off center. Done properly and carefully, it's surprisingly effective providing the stud isn't bottomed out and jammed in.
Removing Broken Studs Using Tools. A variety of tools may be used depending on access. Most work by wedging against the stud and allowing you to back it out. Sears and many others sell the round locking collar type stud remover; Snap-on has a nice but expensive set of locking collet stud removers, sized by diameter and thread pitch, that use remnants of thread. Assenmacher makes a similar socket-like remover that jams onto the stud and allows you to back it out. Warning: these tools may make things worse by snapping the stud off at the head surface, so use care.
Removing Broken Studs with a Torch. [Ted Yaffo] I remove exhaust manifold studs all the time and have found for a stud that protrudes a reasonable amount above the head surface the easiest way to get them out with minimal effort is to use an oxy-acetylene torch handled by a helper or yourself. Heat the head area just around the stud in a CONSTANT circular motion never stopping at any one point for long while the other person using GOOD quality vice grips on the stud works it loose.
Removing Broken Studs With an Electric Welder. [Tip from Gary DeFrancesco] Last spring I removed the head off my '87 745T due to a broken stud. In my case, the stud broke flush with the head, so there was no way to get a wrench on it. Took the head to a head shop and had the machinist replace all the studs, figuring that if one stud is bad, more were ready to let go. The machinist trick to removing the remaining studs was amazingly simple and effective. He hooked up the hot side of his welder to the stud, the ground to the block. Set the welder for about 150 amps., then turned the welder on for 2 seconds. The studs after this treatment are hot to the touch, and the head is a bit warm. But the crud in the threads that makes the stud stick is all burned out. It is the crud that is causing the high electrical resistance. Hence, it is the crud that really heats up and burns off. With the rcrd burned off, he is able to easily unscrew the stud. He finds better than 90% of stuck studs can be removed this way. And there is no warping of the head since the heat is pretty much contained to the cruddy threads and is only applied briefly. Just one of those welder tricks I have filed away for the day when I get a welder.
Another trick you can use if you have a welder is to select a nut with a hole large enough to pass over the stud. Lay the nut over the stud and then fill the hole with weld metal. Then simply screw the stud out with a wrench. Or butt-weld a piece of welding rod onto the end of the bolt so that you can turn the assembly with pliers. [Jeff Goggin] Using a welder, slowly build up a bead of weld on top of the broken stud, until it clears the surface of the head. Using vice grips, grab the weld and twist out the stud remains. I used an oxymig at the slowest wire feed (basically dropping weld beads onto weld beads), and a medium high setting (110v 30amp welder) - ground clamp to the #1 cam journal. Allowing each bead to cool before adding more material, is the key to getting this right.If the weld breaks before the stud would break free, just keep going at it, rewelding until the stud breaks free. This may take over 6 applications of the weld bead technique. Use a hammer on the top of the bead each time, tempering the bead, which appears to reduce the chances of shearing the bead off the stud.
This procedure negates any need for the drill and helicoil procedure in which the biggest problem is getting a straight hole and not drilling through to the water jacket beneath.
B. If the stud is broken off flush with the surface or still won't come out, then you need more extensive work.
Tales of Caution.[Paul Seminara] DO NOT, I REPEAT DO NOT EVEN THINK OF USING AN "EASY OUT" (a reverse-fluted broken bolt extractor). The hardened but brittle extractor can and probably will break off in the hole you drill. Or your hole will be off-center. Then, your available options are reduced to pulling the engine and having a machine shop mill out the extractor/old stud or spending 24 hours and a dozen diamond bits to hog out the broken extractor millimeter by millimeter. It ain't fun! [Editor] If you ignore this advice and break off either an extractor or a drill bit inside the stud remains, then you need to take it to a machine shop for precise drilling or for electro-discharge machining, in which an electrical current is used to melt out the extractor and stud.
[Rob Bareiss] If you do break a stud, get ready to pull the head. Don't try to fix exhaust studs in place. [Randy Starkie] A machine shop deals with these problems everyday and are actually pretty good at it. They are not always able to deal with them however if a lot of molestation (for lack of a better word) has occurred prior to their attempt. You would have to remove the head to take it to a machine shop. That isn't all bad. While the head is off they can go through it and check for plane, worn guides, replace the seals on the intakes and lap or grind the valves (valve job). You would basically have a rebuilt head when finished.
Removing Broken Studs by Drilling. [Ted Yaffo] For studs broken flush or inside the head the quickest way to remove them is to first remove the head. As close to center as possible hammer a point to start your HSS drill bit. No need for fancy or costly drill bits. You will find drilling the first straight hole into a flush broken stud to be the most time consuming. Prep work is critical. After that the rest of the holes drill fast and easy. Start with as small a bit as you feel you can use without snapping it. no larger than 1/8 and only use a variable speed quality drill. you do not need or want to do this at high speed. under 1200rpm is plenty. At this point you can attempt to use the 8mm tap to clean out the remaining metal by carefully tapping a bit and then removing so as to not pack metal into the base of the hole. Or you can drill up to 5/16 which is just under 8mm and use your tap at this point. Sometimes with so little left to the stud you can pick its remains out of the hole. With the head off the car, it takes perhaps 15 minutes to remove a flush broken stud using this method.
[Paul Seminara] Got some diamond bits? Got a right angle reversible drill? Got a moto or air grinder tool? Got the appropriate size left hand cobalt drill bit? Got the appropriate drill and tap? With the above tools you can remove the stud remains. However, centering any hole is critical.
Start with the left hand drill bit (smaller than the stud in question, correct size for stud remover) with the drill in R. Maybe the stud will come out maybe not. Make sure you follow the stud and don't go outside the envelope. When most is gone, you can try to peel off the remaining stud threads from the existing hole or simply drill the hole to the correct size for the tap. Clean hole. Tap, clean and insert stud. Done.
[Editor's Note:] See Alden Corporation's Drill-Out power extractor web site for more information on tools and techniques to remove broken or frozen studs: http://www.drill-out.com/ The same caveats apply to these devices as to Easy-outs.
Removing a Stud by Drilling with Diamond Bits. What I normally do when a punch won't remove a stud is drill it with a diamond drill chucked in a dremel tool. This is fast and is much easier to control than a regular drill. The diamond drill is cheap (~$8 from Truebite - check 800 directory assistance) and since it is coated on its sides, can be used as a burr. However, this requires precision. Grind off the end of the bolt perfectly flat, measure the center exactly, and center-punch it hard enough. After drilling the hole, I use the drill to enlarge the hole until it approaches the diameter of the base circle of the threads. Work your way up slowly. Usually when the walls of the stud are reduced to this thinness, the tension relaxes and it can be walked out with a punch or even a screw driver pushed down the hole. If not, I continue to enlarge the hole until I see the threads. Then I pick the remaining spiral of metal from the hole.
Removing a Stud by Grinding Out With a Dremel. [Tip from James Dichter] I went to Home Depot and bought a Dremel with the long hoselike attachment. I removed the exhaust manifold and turbo. Hang the dremel on the hood and use a dremel drill bit on the end of the hose attachment and drill a holl in the stud. Then use the dremel engraving tool and slowly bore out the hole until you have cut away the entire stud. Now that you have the hole and you've removed most of the threads simply retap the hole with new threads with a tap. Important!!!! When tapping aluminum go very slowly in and out: 1/10th or a turn in and out seemed to do it. (aluminum is soft and tends to blister if you tap a hole too quickly) After you tap the hole or holes insert new exhaust studs, attach the gasket and reassemble
Removing a Broken Stud by Drilling: General Tips. [JimL] If a stud breaks off, you can drill it out and retap the hole. Procedure for drilling a stud out is as follows:
- Safety. Wear eye protection. Get a good full face shield if you do this with it still in the car. I spent an evening, new years eve, in the ER having them fish bits of manifold stud out of my eye, all due to a few pieces going in from under my safety glasses.
- Drill Bit Size [George Downs]
An 8mm stud is 0.315" in diameter, a 17/64" bit is 0.266. If the stud is 8mm an 8mm drill will drill
all the threads out of the hole. Tap drill size for 5/16"-18UNC is an "F"
drill which is 0.257" and the threads are only SLIGHTLY bigger so I would
stick with 17/64 or maybe slightly smaller. A "G" drill is 0.261" and would
probably be an appropriate tap drill. You might want to start with a ¼" (0.250")
drill and see how it goes. All the above is based on the stud being 8mm. If it is a smaller size (6mm) you will ruin things with either drill. - Make sure top of stud is flat or nearly so. If necessary, grind/file the top of the stud flat. With a SHARP centerpunch, carefully punch the stud in the EXACT center. Using a NEW 3/32 or 1/8 bit, carefully drill down through the center of the stud, checking carefully as you go to keep the bit centered. Pull the bit out every so often and cool it in oil as you go. Replace the bit with a new one as it dulls. An alternative: use a left-handed drill bit that rotates in such a way as to apply force to unscrew the old stud while you are drilling the hole. Once you are all the way through, enlarge the hole with the next larger sized bit, increasing by no more than 1/32 or 1/16th inch. Eventually you will have drilled out to the root of the threads. Retap the hole, and install a new stud or use a cap screw (bolt) instead. You may have to drill and tap for the next larger size stud. It is difficult to drill precisely in the center of a small stud. The secret is to go slow, check often, and use SHARP bits. Also using a variable speed drill helps. [Randy Starkie] I've had some success by inserting a short piece of steel tubing into the manifold hole and using it as a sort of drill guide to keep the drill centered on the broken stud. If the center of the manifold hole isn't in line with the center of the stud, this becomes a bit more difficult - you then start looking for ways to shim the tubing off to one side or the other.
- It's not really a difficult process - just tedious.
Removing a Broken Stud with a Right-Angle Drill. [Tip: Bob Mohr] Been there, done that. A right angle drill will work just fine. I'd suggest using a diamond bit in a Dremel rotary tool to put a nice, centered starting dimple in the middle of the broken stud to prevent the bit from walking once you start. Taking care to center the bit, drill or punch will save a lot of work later digging out threads from an off-center hole. You shouldn't have to buy a special diamond tipped drill bit. I went down to the local industrial supply and purchased a cobalt bit that went through that old stud like a hot knife through butter. Why cobalt? Normal hardened HSS, or even the TiNi drill bits won't touch that stud!! Have a bottle of cutting oil nearby and squirt a little in the hole every quarter inch or so to cool the bit and flush out the shavings. I ended up drilling it out oversized and installed a helicoil. It worked great.
Another tip if you don't have a right angled drill. I used one of those fiberglass reinforced cutoff wheels in a dremel to reduce the length of my cobalt drill bit. You have to be careful chucking the drill bit, as it's tough to get it in straight. Cutting down the drill bit gives you just enough clearance to get a straight shot at most of the studs with a plain Jane 1/4" drill.
Removing Broken Studs by Heating the Head.
[Tip from John Sargent] My wife's 86 745T had several broken exhaust studs. I was able to drill and remove all broken studs but one. In order to remove it, I pulled the head and put it in the kitchen oven, at 225 degrees F., for about 45 minutes. When I pulled the head out, it was at about normal operating temperature. The broken stud came out with torque that would not remove it at room temperature. The thermal coefficient of expansion for aluminum is very close to six times that for steel. Now the kitchen smells like an automotive machine shop. If you choose to use this method, I don't recommend locally heating the head, as you might warp it.
Replacing the Studs: [Dick Riess] Have done it with the 90 degree drill, unfortunately w/o diamond bits and kinda made a mess, but my machine shop friend let me use his Time Cert outfit to fix it. Evidently the Time Cert is used extensively on hopping up the old aluminum VW engines. They just don't come out. So if you mess up the threads, there is still hope.
Replace Studs with Stainless?
[Response: John B ] If you break one stud in the process, you might as well replace them all. Almost any stainless alloy is going to be weaker than a good steel alloy...it's only advantage is it's supposed to be proof against corrosion. But you're not a marine environment, so I'd go with stock steel studs. Helicoil the heads if you must, but you'll get higher clamping forces with the stock studs.
[Tip from John Sargent] Volvo has a service bulletin to replace the exhaust manifold studs with the new part number. The new ones are supposed to be better, and for about $2.30 each, not a large expense. Note that turbo studs may differ from non-turbo studs: make sure of your part numbers.
Use of Thread Adhesives.
[Inquiry:] Several of the exhaust studs unscrewed from the head and will need to be reinstalled. Since this is an aluminum head should I use antiseize or some Loctite? Will anything take that heat anyway?
[Response: Tom Irwin] I'd get new studs and re-tap the holes. Then I'd use a high heat removable Loctite, designed for dis-similar metals.
Use of AntiSeize. Coat the new exhaust manifold nuts with high-temperature nickel-based antiseize.
Loose Studs Require Helicoil. [Tip] If your stud is loose, first get the appropriate tap and try to clean out the hole. Then try to screw a stud or bolt in there and see if it holds. If not, you can reinstall it using a Helicoil. There is plenty of room in the exhaust manifold ear to drill the hole. The holes are .440 except for the locator ear top of port #3. The helicoil that fixes M8 requires a drill diameter .328. You might have to cut the 21/64 bit to get it head on with a standard drill motor without resorting to a right angle drill, but that depends on which stud is stripped. Since the stud is not broken in the hole, drilling and tapping should be effortless. Helicoil (not TimeSert) is the recommended fix per Volvo's manual; it is done all the time and if you drill straight there's nothing to harm surrounding the tapped hole. If you decide to fix without 8mm helicoil, make sure you use a hardened stud or bolt and not all-thread or similar. The turbo engine uses different studs vs. non turbo per parts manual. [Jeff Pierce] With the stud removed, take a piece of aluminum foil, and wrap it (counter-clockwise) around the threads that will be inserted into the head. Insert the stud as usual. What this does is puts some aluminum (same material as the head) into the slightly over sized hole to fill in for the damaged threads. Because it's soft and thin, it capitalizes on the remaining threads in the head, giving the stud something to bite into.This works only for low-torque installations, which is the case here. [Fitz Fitzgerald] An alternative is to find one stud size larger and drill/tap to install this in the head instead of using the original size stud and a Helicoil.
Exhaust Stud Nut Re-use?
[Tip from Bob] Do not re-use exhaust manifold nuts; use new Volvo flanged copper nuts. Reuse the original concave Volvo steel washers under the nuts: the concave side faces the head. Replace all three exhaust manifold-to-down pipe lock-nuts when replacing the gaskets. These nuts are not to be re-used
[Jim McDonald] Use P/N 94560A080 from McMaster-Carr instead; they're stainless so they won't sieze, and they're locking so they won't loosen. If you use aftermarket nuts, they may not be flanged: a copper washer will help secure the nut and stud. [Cameron Daline] ATP Turbo sells a copper nut that works well for only about $1 each.
Removing the Manifold and Replacing the Gaskets. [Tips from Turbobricks, John Sargent, and others] Place the front of the car on jackstands or ramps: you will need good access to the underside. Remove all the manifold nuts and loosen the down pipe nuts OR loosen the down pipe fixing bolts at the bell housing and transmission, depending on your car.These will be rusted, so use LOTS of penetrating spray for a couple of days before. Use the old trick of first tightening a little, then loosening. Heat often helps. Loosen the EGR pipe into the back of the manifold, if so equipped: this pulls back about a centimeter, but is invariably rusted. Use penetrating oil, Vice Grips to twist slightly, and a piece of wood and mallet to knock it loose. For turbo engine complexities, see these notes. Finally, you may have to push or pull the engine toward the driver's side to clear the exhaust manifold studs: use a jack beneath or a puller on the top engine lift at the thermostat. The exhaust manifold gaskets fit into each manifold runner. Needless to say, you should replace all four. If you look closely at the exhaust manifold gaskets you will notice they are not symmetrical: one side is flatter. If the exhaust gasket are rotated 180 degrees when installed, they will burn out in a month or two. Watch how the old ones were fitted. Or just fit them so they appear to match the ports. Each OEM gasket should be stamped "UT" which means "out"; that side (which is the metal side) faces toward the exhaust manifold and away from the cylinder head. The softer fibre side goes against the cylinder head. The Volvo OEM exhaust gaskets, by the way, are of superb quality. The exhaust manifold gaskets fit into each manifold runner and are located by the studs. Needless to say, you should replace all four. Do not use any sealer, but re-coat the stud threads with nickel-based high-temp antiseize. Reinstall the thick cupped washers with the concave side against the manifold in the recesses provided. Replace the spark plug heat shields: these prevent exhaust gasket leaks from ruining your plug wires. Retorque to 10-20 ft lbs (14-27 Nm) for B230F/T, 15 ft-lb (20 Nm) for B234F, 7-11 ft lbs (10-15 Nm) for B280F.
B6304 Engines. [Walt Poluszny]The six cylinder engine has six separate gaskets (one for each runner) and Volvo recommends a sealing compound. An effective aftermarket compound is Silkolene 762 available from racing shops. Torque the bolts to 18 ft.lbs. I would re-torque after at least one heating/cooling cycle. There's no gasket between the exhaust manifolds and the head pipe. To remove all bolts, I would soak the bolts with a good penetrant the night before (and again in the morning) and only use a 6 point socket. Volvo uses good bolts, they'll come out fine if you take your time.
Leaks in Manifold to Downpipe Joint. This joint has a small gasket (non-turbo engine) which can fail. To remove it, you must remove the special flange nuts on the studs. Be careful removing these nuts since the studs may break. [Walt Lear] Spray them down with some PBlaster, drive it and get them hot. Then spray again wherever you are going. Do this for a couple of days. Usually come out like butter. [Matt Henning] I treated the nuts on multiple occasions with a healthy dose of PB Blaster. I had my reservations as the threads on the studs looked pretty rusted over. I gave them a final dose of Blaster and zapped them with an impact wrench. They came right off. I did not want to break the studs using a breaker bar and socket and the impact wrench worked well. [Inquiry] How do I replace broken studs between the exhaust manifold and the downpipe? (Note: if you have a turbo, see this section.)
[Rob Bareiss] If a stud on the manifold breaks, it's not as bad as fixing a stud in the head. You can drill right through the manifold to replace them. The flange is exposed on the top side, so you can drill it out and re-tap for M10, or use any bolt that fits the hole. I'm not recommending that a through-bolt is necessarily the best repair, but it will work, and I've seen cars with that fix for a long time. However, in my experience, apply PB Blaster over the course of a few days before attempting the repair, and the nuts will most likely come off OK. Careful with the rear one, it's a bit more of a challenge to get at. Expect to have to apply a pretty strong force to break these loose. Original nuts are 16mm. Replacements could be 15, 16, or 17. Get new copper M10 nuts from FCP Groton or another supplier before starting this job.
Exhaust Brackets Keep Breaking.
[Inquiry:] 've replaced the exhaust bracket about three times during the past 5 months every since I replaced the system. The bracket keeps on breaking/splitting at the same exact point all the time. Does anyone know why this is constantly occurring?
[Response: Paul Grimshaw] Check your motor mounts. Bad mounts can put greater torsional strain on the pipes. If they're sagging or twisted, replace both of them. Also suggest changing the tranny mount at the same time. Next, loosen all of the pipe joints, replace your bracket. Now lightly wiggle the pipes to find their (untensioned) resting point. Make sure that no areas of the pipe are touching the chassis. Make sure that at full droop, your 740's rear axle is not hitting the cross-over pipe. Now tighten things up carefully.
[Response 2: Dana] Make sure you still have the spacing ring in between the two pipes and that all the exhaust flanges are in place and not stretched out to far. I had a problem with my bracket and clamps loosening up every 1000 miles or so. Turned out the bracket was a manufacturing defect and the clamps I used couldn't hack it.
[Norm Cook] On the exhaust downpipe, there's a 1" wide strap that fastens the pipe to bell housing bolt. Mine had cracked all of the way through on both sides of bolt hole so it wasn't holding pipe at all and caused an exhaust rattle. This is important to fix as not having it secured at downpipe would place extra strain on the various exhaust and turbo parts.
[Tom Kaylor] I think this could be a design error: I broke three of these. Look for failures here.
Exhaust Manifold Cracks and Repairs.
[Inquiry] What would be the best way to repair a 90+ turbo exhaust manifold? It is cracked on the backside where the pipes all intersect (area looks like an X).
[Response: Phil Bradley] It is best to find another uncracked manifold. I was told by my machine shop, which is very good, not to bother welding; it would most likely be a temporary repair. If the crack does not yet go all the way through, it is not leaking yet and you may have some time. In that time, get a better one. The 90+ turbo manifolds are prone to cracking. There is some information at Muggy Welding about welded repairs. But realize that there are cast manifolds that see 1200 degrees and there are cast manifold that see 1800 degrees. Turbo manifolds will more likely be the ones seeing 1800 degrees. According to Muggy Welding, turbo manifolds are problematic. While his rods have worked extremely well on non turbo exhaust manifolds, he has had at least one failure on a turbo manifold.
Painting the Manifold? [Tip from Tom Irwin] Don't paint your exhaust manifolds, even with hi-temp paint, no matter HOW COOL it looks! The paint burns off under the bolt heads and relieves bolt compression. Almost ALL were under torque spec. [Editor] Probably OK to paint IF you don't paint under the bolt heads.
Repair to Catalytic Converter/Engine Pipe Joint Cracks. Split Flange [Tom Frisardi] To repair cracks at the converter/engine pipe joint or rusted bolts, you do not need to replace the components. Volvo sells the flanges for the converter and engine pipe separately from the converter and pipe, but in split form: they are split axially and tubes are welded to the outside to enable the two flange halves to be fastened with bolts. This clever fix cost me around $15 vs. over $500 for the converter and engine pipe. Volvo p/n: 8551977 for the flange. The pic right shows a NAPA version (p/n Balkamp 732-1137) of the replacement split flanges. Sealing Ring Requirement. [Bruce Young] I recently recently replaced OE Front pipes on '92 and a '93 940s.
Both had the "bell mouth" junction at the cat and needed a sealing ring. Make sure you get the ring appropriate for your exhaust: turbo is Volvo p/n 1306852 and non-turbo is 1266118. FCP Groton gets $3.99 for aftermarket version (1991-1995)Aftermarket Mushroom Shaped Joints: No Sealing Ring. In some cases, the ends of the pipes may be formed in a mushroom shape and not require a ring gasket. Bosal, for example, makes cats and downpipes with these shapes that mate with each other and do not employ a sealing ring. [Removal and Installation] [Mike H.] Getting the bolts off the flanges can be a nightmare. Don't hesitate to use an acetylene torch. To remove the old rusted flange, merely cut it away. Often these joints leak on installation because the pipes
are not aligned correctly. Clean up the joint with a wire brush and sand paper to smooth out the surface of the bulb/socket. You need to rock or brace the exhaust as you
tighten the joints to ensure a proper seating.
Upgrades:
Stock or Performance Exhaust System? [Dick Riess] The advertising would have you believe that larger cat back exhaust systems are a real help on MPG and performance. My experience on two different cars tends to show no difference except for significantly increased noise levels in the vehicle and outside with the sport system. First car was an 87 740GLE NA. I put a 740 turbo exhaust, cat back. Had to have the cat welded to the first muffler and there are no adaptors. No difference noted except interior noise. Replaced with stock this past weekend. Next car was a 93 940 T which I put the IPD sport exhaust on. The noise level was terrible. No real changes in power or MPG. Gave it to son-in-law for his turbo wagon and replaced mine with stock. Son-in-law took it off his car and sold it. Bottom line: Volvo makes a good exhaust system stock. Unless you get into serious performance issues or like noise, stick with stock and save your money
Exhaust Upgrade [Jerry Casey] 940T, 260k. Original exhaust, which my friend who has a 760T noticed was the same diameter pipes as the nonTurbo, 50mm. So, knowing of my quest for the Grail, I mean power, and after reading some of StealthSTI's musings about performance and the exhaust systems he did for some of his rebuilds, that getting gases Out is as important as getting them In, and due to holes in the muffler saying 'it was time', we entered... the PnP zone.
We saw various 7 and 9 cars but most had the same size pipes. Then there were some S90 cars, one of which had a very good looking set of pipes. So to speak. 60mm, with a great resonator and the Huge rectangular muffler, which at first glance looks like it couldn't fit. But he measured and was sure it would fit. So:
It fits very well. The basic body shell is the same between the models, and the S90 has the indy rear, so the pipe over the axle has even more room. I had taken the aluminum heat shield and brackets on the car also but didn't need them as they're all the same. All hangars line up correctly. The muffler shop I had put it in did a great job, making a new pipe over the axle which we had cut badly taking it out. If we had more room to get at it at the pnp I would have needed no new parts. The only thing not stock was to weld an adapter to fit the pipe on the back of the cat.
Power increase is...dramatic. Low end takeoff is nicely improved, and it runs through the gears with alacrity. Very modest throttle gives immediate results, in a not unpleasant manner. It is the single best performance thing I have done. This was a remarkably simple power mod that fits and works, and in addition the car is now virtually silent, eerily so, even when flying by. The only issue is that my tow bar doesn't fit, I need the S90/V90 one due to the much larger muffler. And I am eager to see how or if mileage is affected; will report back about that.